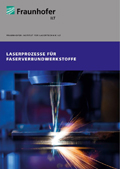
Für die großserientaugliche Anwendung von Faserverbundkunststoffen (FVK) sind geringe Herstellungskosten und kurze Zykluszeiten ein vorrangiges Ziel. Die Bearbeitung dieser inhomogenen Materialien erfordert dabei Prozesse, die an die Anisotropie des Werkstoffes angepasst sind. Aufgrund seiner Flexibilität, der Verschleißfreiheit und der hohen Bearbeitungsgeschwindigkeit ist der Laser hier das ideale Werkzeug. Das Fraunhofer ILT entwickelt im Zentrum für Laser-Leichtbau Laserprozessefür FVK Komponenten, welche die spezifischen Eigenschaften der Werkstoffe nicht verändern und deren Vorteile optimal erhalten.