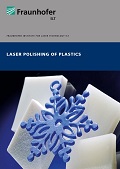
As the use of Additive Manufacturing of plastics continues to grow, so does the demand for flexible finishing processes. To meet this demand, the Fraunhofer Institute for Laser Technology ILT researches and develops new processes and processing strategies specifically for the laser polishing of plastics. Furthermore, laser polishing also provides flexible and efficient solutions for injection molded components, prototypes or plastic optics – solutions that ar e tailor -made for customers fr om industry and research.