Our range of services
In the process from development to delivery, a lot of information about a product is generated. The higher the number of components and processing steps, the larger the database becomes over time. At that point, it is usually difficult to grasp the relationships and influencing factors at a glance. In this context, the concept of the digital Twin plays a central role.
The digital twin comprises the virtual model of the process by collecting and analyzing the real data. Influencing factors can now be easily identified and cause-effect relationships can be revealed without intervening in the real process. The digital twin, therefore, enables users to better control complex production processes and their cause-effect relationships.
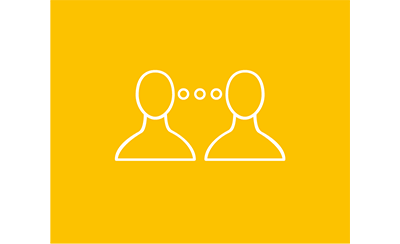