Potential of LPBF in production
For more than 25 years, the Fraunhofer Institute for Laser Technology ILT has been continuing to develop process control, plant and system technology, as well as applications for the additive manufacturing process laser powder bed fusion (LPBF). The institute’s LPBF Application Development group supports you in transferring the latest findings from the laboratory to existing production processes in your industrial manufacturing. Our experts work on an interdisciplinary basis with partners from industry and research.
Since it applies layer upon layer using CAD data, LPBF can produce highly complex components from metallic materials without the need for forming tools, complex components that cannot be manufactured with conventional processes such as casting or machining. LPBF thus offers users a number of systematic advantages:
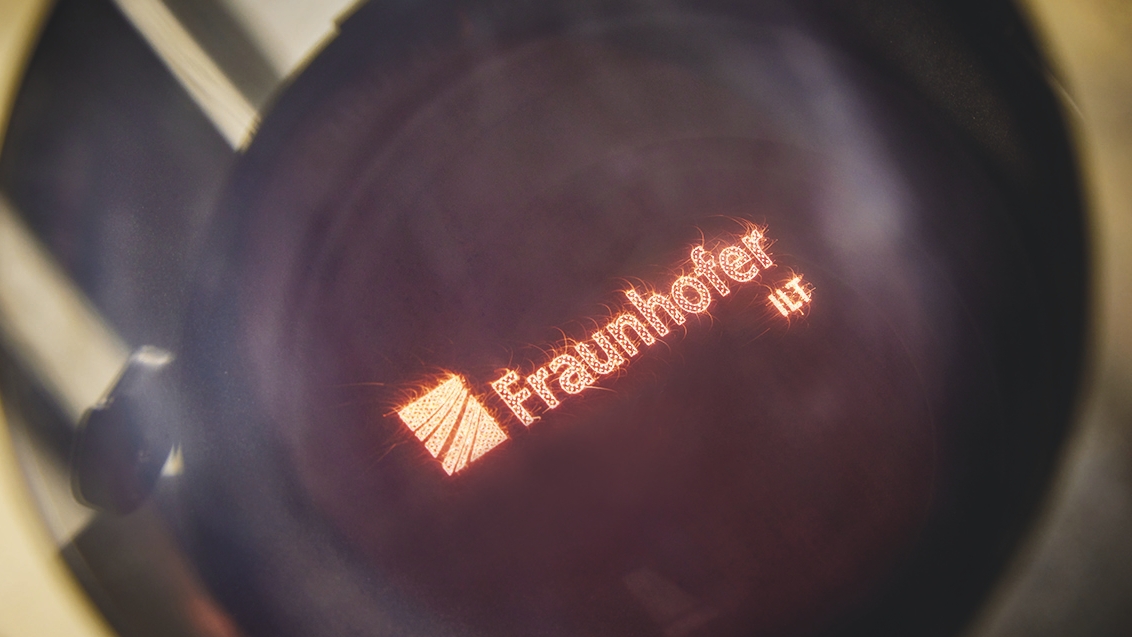