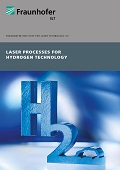
Green hydrogen is the energy carrier of the future as it shows great potential for applications in mobility and domestic energy supply based on fuel cells. While further technological developments are required, hydrogen can only penetrate these markets when costs are reduced along the value chains of electrolyzers, fuel cells and their components. To accomplish this, highly productive laser processes play a decisive role in scaling up manufacturing pr ocesses.