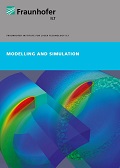
The Fraunhofer Institute for Laser Technology ILT engages in fundamental work on the description of technical processes as well as their monitoring, control and regulation. With the combination of a deep physical understanding of laser processes and modern computational engineering techniques, Fraunhofer ILT provides the basis for tailor-made laser processing.
Our core competences include the modelling of radiation sources – in particular, high-power lasers and gas discharges – as well as their application in manufacturing technology. The involved physical processes range from generation, propagation and absorption of radiation to transport processes and phase transformations induced in the material by radiation. We apply methods of computer engineering to analyse the measurement data and to monitor the processes. These include, in particular, numerical methods for simulation and visualization of the processes as well as algorithms for interpretation of measurement data.
Our experienced team includes researchers in the areas of applied mathematics, physics and computer engineering. Together, we offer our customers model-based solutions for technical tasks. We develop and analyse individual approaches based on the knowledge of our customers and our expertise as well as the properties of existing models.