LPBF - Next generation manufacturing technology
The manufacturing industry is facing many challenges: resource scarcity and uncertain supply chains as well as growing demand for individualized products. In addition to economic considerations, ecological aspects are coming to the fore in the manufacture of goods. Additive manufacturing processes offer solutions to these current challenges.
Since it applies layer upon layer using CAD data, LPBF can produce highly complex components from metallic materials without the need for mold-bound tools, components that cannot be manufactured using conventional production techniques such as casting or machining.
The LPBF Application Development group at ILT supports customers who want to begin using this technology, to plan their production and develop their processes, as well as those who wish to design components compatible with AM. We have access to an extensive and modern industrial machine portfolio – from µ-LPBF machines with extreme resolution to large-scale systems with 400 dm³ building space.
We already offer our customers the machine technology of tomorrow thanks to our close internal cooperation with experts from optics design and beam source development, as well as from LPBF process and machine development.
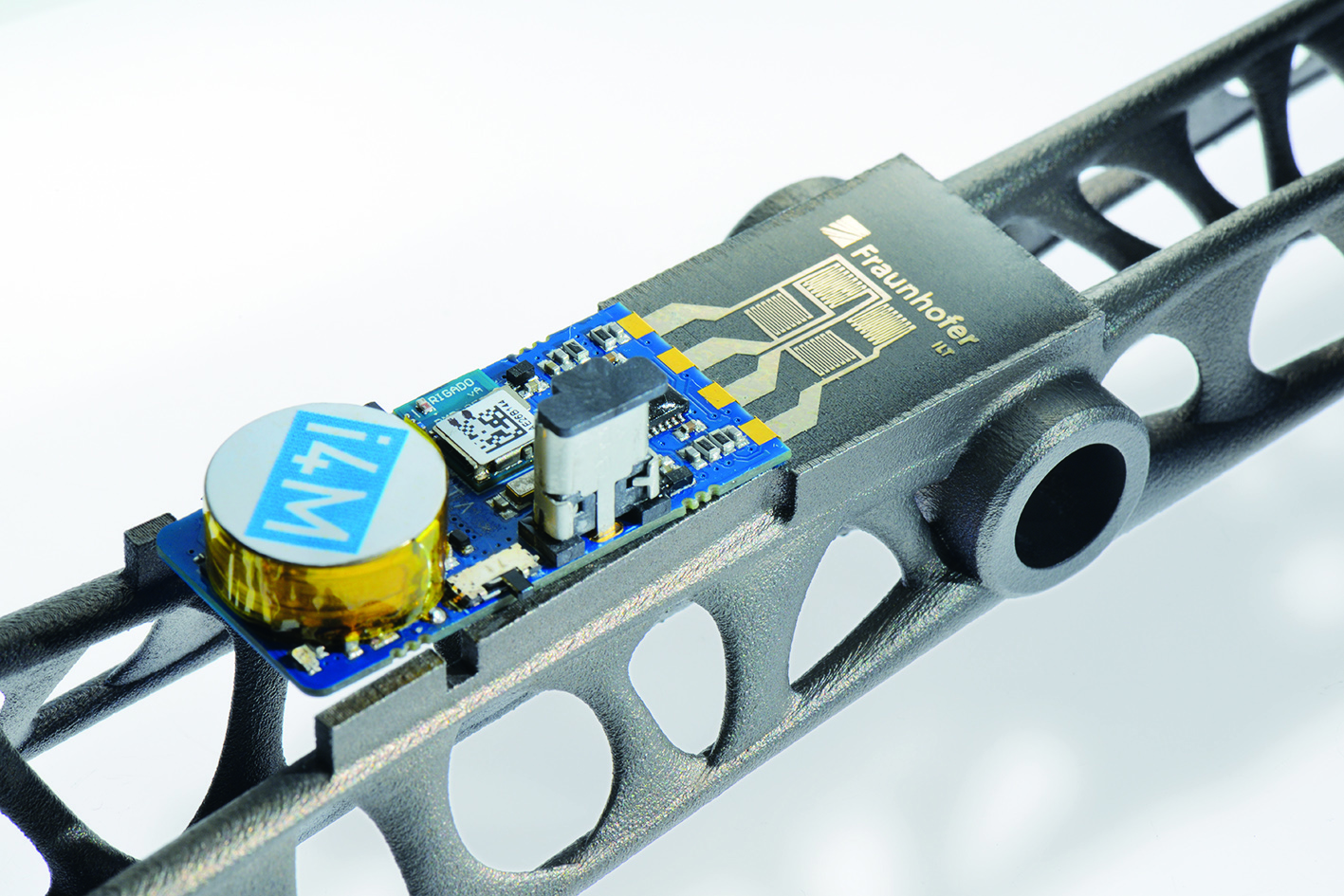