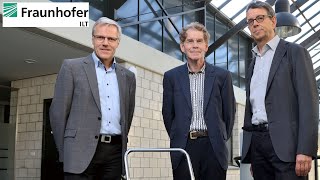
Privacy warning
With the click on the play button an external video from www.youtube.com is loaded and started. Your data is possible transferred and stored to third party. Do not start the video if you disagree. Find more about the youtube privacy statement under the following link: https://policies.google.com/privacyA Defining Patent: 25 Years of Metallic 3D Laser Printing
A drone hovers in the sky above the Fraunhofer ILT. It films 50 employees from the “Laser Powder Bed Fusion (LPBF)” department from above as they stand together and form the number 25. The anniversary of the basic patent for LPBF marks an occasion for a video clip: 25 years ago, only one Fraunhofer ILT researcher was actively working on the project and the patent for metallic 3D laser printing was filed in 1996. “This is an auspicious occasion for a retrospective and outlook on our technology,” Jasmin Saewe says, pleased. She has been head of the LPBF competence area at Fraunhofer ILT for several months. Today, she is in charge of around 50 employees and students.
Further information: